
NASA借助3D打印技术实现经济实惠的火箭发动机制造
宣布时间:
2023-01-11 12:45
早在2014年,当NASA首次实验用铜制造火箭发动机部件时,工程师们也担心他们可能会浪费时间。然而,最新的结果证明,铜金属的3D打印翻开了实现经济实惠的火箭发动机制造的又一扇大门。
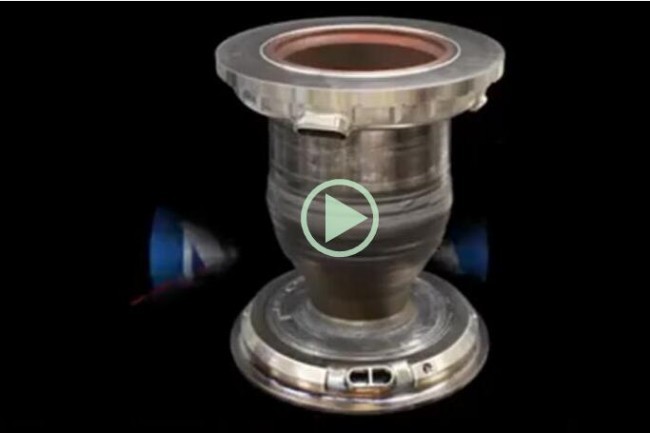
视频:NASA的LCUSP项目。来源:NASA
庞大的冷却通道成绩下一代发动机
铜似乎不适适用于3D打印来加工,因为这种金属容易直接反射3D打印机的激光束。铜金属在激光熔化的历程吸收率低,激光难以连续熔化铜金属粉末,从而导致成形效率低,冶金质量难以控制。
继2016年和2017年,NASA 在马歇尔太空航行中心对3D打印的GRCop-84组件进行热火试验后,该团队开始开发GRCop-42。NASA 希望通过该质料具有与GRCop-84相似强度,但具有更高导热率。NASA 研究人员体现,通过该质料制造的增材制造发动机燃烧室组件将“凌驾古板方法制造的上一代产品”。
凭据NASA的LCUSP计划,NASA的铜基和镍基合金3D打印技术已经生长到这些技术所制造的零件通过热火试验。
不过3D打印铜合金所制造的燃烧室所面临的一大挑战是如何经受住6,000华氏度的火箭燃料燃烧。为了避免铜过热,火箭工程师设计了具有庞大微小通道的燃烧室,通过泵送冷却剂来实现散热,从而坚持温度平衡,包管发动机不受损坏。
铜合金燃烧室零部件内外壁之间具有200多个庞大的通道,制造这些微小的、具有庞大几何形状的内部通道,纵然对增材制造技术来说也是一大挑战。部件打印完成后,NASA的研究人员使用电子束设备为其涂覆一层含镍的超合金。
这些庞大的通道通过古板制造工艺来实现则相对较慢且本钱较高,3D打印将永远改变这一点。NASA通过GE旗下的Concept Laser的选区激光熔化设备实现这些庞大的内部通道,并使得火箭发动机的设计越发紧凑和轻量化。
挑战仍然保存,3D打印的腔室壁和内部冷却剂通道仍然不像NASA研究人员所希望的那样平滑,目前NASA正在进行若干实验以平滑这些通道,或者通过革新打印历程找到更好的要领来平滑外貌。
NASA的成绩来自于其在质料和火箭科学领域的跨界结合,NASA位于俄亥俄州的格伦研究中心中,质料科学家在铜中添加一点铬和铌可增加金属强度和抗疲劳性。
NASA的最终目标是要是要使火箭发动机零部件的制造速度大幅提升,同时至少降低50%的制造本钱。
3D科学谷Review
凭据3D科学谷的市场视察,多家制造企业在开发铜合金3D打印工艺。海内金属3D打印企业铂力特已在铜金属激光成形领域取得了进展,研制出针对难熔金属和高导热、高反射金属的3D打印工艺,实现了庞大流道的铜质料制造工艺,乐成制备出3D打印铜合金尾喷管。
国际上,Aerojet Rocketdyne在火箭铜合金推力室3D打印领域取得的突破,为制造新一代RL10发动机带来了可能性。3D打印铜合金推力室部件将替代以前的RL10C-1推力室部件。被替代的推力室部件是由古板工艺制造的,由多个不锈钢零件焊接而成,而3D打印的铜合金推力室部件则由两个铜合金零件组成。
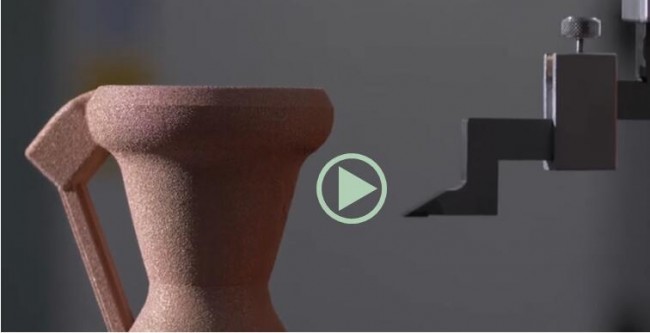
视频:3D打印铜合金火箭部件的全历程。来源:Launcher
首创的航天企业Launcher 与相助同伴3T、EOS 也开发了3D打印铜合金火箭发动机部件,3D打印技术的应用可以减少发动机零件数量,缩短开发时间,并且越发易于制造庞大功效集成的部件,Launcher 开发的3D打印铜合金(Cucrzr)发动机部件就集成了庞大冷却通道,这一设计将使发动机冷却效率获得提升。
关于铜的3D打印用激光器,凭据IDTechEx Research 的《激光二极管与直接二极管激光器,2019-2029 年:技术、市场与预测》报告,已往 30 年来,激光二极管的平均功率显著提升,而每瓦平均价格却呈指数级下降。因此,激光二极管正在取代一些已有的激光和非激光技术,同时也使全新的光学技术成为可能。
2018 年,岛津公司拟(日本)实现了其 BLUE IMPACT 蓝光攻击二极管激光器的商业化,。岛津 450 纳米蓝色二极管激光器的一个要害应用是铜质料的 3D 打印。铜对蓝色激光的吸收率很高,背反射的减少可以使加工历程变快,这对古板的红外激光器是一个严峻的挑战。新研发的 3D 打印机可以用纯铜粉高效打印物体。现有的3D打印机技术一般接纳 CuCr1Zr 等铜合金来取代纯铜。
IDTechEx Research 预计,随着更多产品的商业化,从 2019 年起,蓝光 DDL 将会很快应用于铜加工领域。(来源:3D科学谷)
3D打印技术,3D打印,增材制造